A Puppet for Language Education
- paradoxicallisa
- Nov 9, 2024
- 4 min read
This isn't actually a new project. It was initiated around November of 2023 and completed a few months after. But it was only recently delivered to the client, and now that they have accepted it I'm more free to showcase the project.
This project was commissioned by a language education program called Bilingual Village that were looking for new creative new elements to add to the program. After some discussion, we concluded that I would create a set of props to serve as visual aids accompanying stories about real-life experiences by young people immigrating to new countries. Along with the props I would develop a mascot for the program which would take the form of a puppet and assorted collateral items.
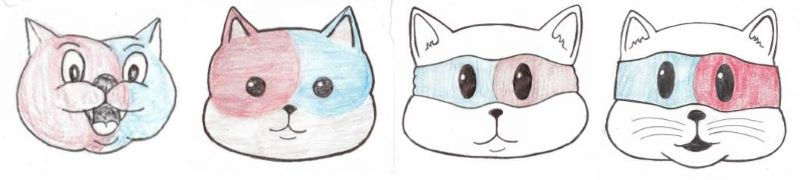
The first step for developing the mascot was to come up with a concept. we were starting from a blank slate, so the options were wide open. I started by looking at their existing branding. Their logo consisted of two overlapping dialogue balloons, one read, one blue. Maybe its the cat person in me, but I noticed that if it was flipped upside down, it would resemble a cat's head. That called to mind the idea of a Calico cat, with red and blue color spots on either side of its face. I did some concept sketches and pitched it to the client. They loved the concept, but one of their members suggested the idea of a super hero style character with a red and blue mask rather than the colors being in the fur. So I drew up a few more concepts around that idea, and we incrementally narrowed down the design. Once it a final design was approved, I moved in to the fun part, which was the actual fabrication.

This started with carving a full scale form of the mascot's head from a block of EPS foam (i.e. "styrofoam"). That allowed me to create a pattern by covering the form in painter's tape, and drawing out the pattern pieces with a silver sharpie. I really enjoy the patterning stage. It takes time and practice to understand how curves and forms translate to flat pattern pieces, and then back again. But once you have this down, it really opens up infinite creative possibilities with foam fabrication.

Pattern made, I could then start cutting out the pieces from the EVA foam. And I should note that I chose EVA foam for this because it is what I was familiar with. But in hindsight it was not the right material for the job. It has the light weight I needed, but I found it is much too rigid for this purpose. I'll take that as a lesson learned for the future. The construction stage went quickly, with EVA foam pieces connected using contact cement. It's very satisfying to see a piece take shape like this.

Next up came the hardest part for me; which is the sewing. As I've noted in my cosplay posts, sewing isn't my strongest skill. So I knew this would be a challenge, but not outside my ability. One fortunate thing was that I could use the same pattern I used for the foam construction for cutting the fabric pieces for the "skin" of the puppet's head. It just needed some allowance for seems and accommodation for adding the kitty's ears. The actually came together pretty quickly, with the only really challenging area being the jaw. Figuring out how to allow for movement while minimizing the visibility of seems.

The second part of the sewing stage was creating the body. The client didn't ask for any articulation of the arms, so it was essentially a sleeve that would attach to the base of the puppet head. That allowed for the operator to insert their arm and manipulate the head and jaw movement with their hand like a sock puppet. Following the superhero theme, I gave the puppet a shiny silver super suit, which would also include a logo on the front. Additional white fur would be visible at the neck and hands. The silver fabric was very silky and delicate, which resulted in a few mishaps. I still have a few rejected attempts at making the arms here, which have become the favorite toys of my real life kitten. They eyes and nose were shaped from scraps of EVA foam, and would get a gloss coat for the final piece.
At this point, the hard work was finished and it was all a matter of adding the final details. I sewed the two-toned mask, and simply added the eyes to the outside of the fabric rather than trying to create eye-holes. And after a few iterations, the client and I settled on a final design for the logo, which I 3D modeled and printed in flexible TPU. To attach the TPU to the puppet, I sewed a piece of pleather onto the front the torso, then used CA glue to attach the TPU to the pleather. That created a more reliable bond than trying to glue the TPU directly to fabric. I did have a panic moment here, when I drop of glue fell onto the silver fabric. I was able to wipe it away, but it left a spot. Thankfully, I discovered that acetone was able to remove the CA glue without dissolving the fabric (I tested this on a scrap of fabric first to be safe). So there is hardly any sign that the accident ever happened. Whew.
Comments